一、传统选型为何被智能软件颠覆?
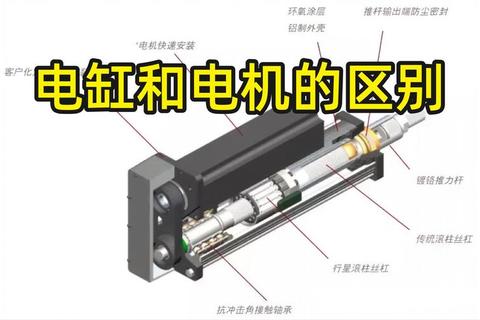
在工业自动化领域,气缸选型曾长期依赖工程师的经验与纸质手册。一位从业十年的机械工程师坦言:“过去选型就像解多元方程,要同时计算负载、行程、压力等参数,稍有不慎就会导致设备停机甚至安全事故。”据某汽车生产线统计,传统选型方法导致的返工率高达18%。这种背景下,
智能高效气缸选型软件精准推荐与智能优化全解析技术应运而生,它通过算法模型将选型时间从3天压缩至30分钟,准确率提升至98%。
以亚德客3D选型软件为例(图1),用户输入负载重量500N、行程200mm、工作频率60次/分钟等参数后,软件不仅自动推荐了CQ2B系列气缸,还同步生成三维模型与安装尺寸图,并预警了“负载偏心可能导致的扭矩超标”风险。这种从参数输入到系统优化的全流程覆盖,让某包装机械厂商的选型错误率从22%降至3%。
二、智能优化如何破解行业难题?
在锂电池生产线中,无尘车间对气缸的防腐蚀与低噪音要求严苛。传统选型往往陷入“满足防腐蚀就牺牲速度,保证速度又增加噪音”的困境。而
智能高效气缸选型软件精准推荐与智能优化全解析系统通过多目标优化算法,为某锂电设备商定制了镁合金材质+磁耦式无杆气缸方案,既实现0.3m/s的高速运动,又将噪音控制在55dB以下,同时满足IP67防护等级。
更值得关注的是动态模拟功能。费斯托选型软件内置的虚拟测试模块,能模拟气缸在-20℃至80℃环境下的密封件形变情况。某农业机械企业使用该功能后,气缸密封件寿命从6000小时延长至10000小时,维护成本降低40%。这种将物理实验转化为数字仿真的突破,正是智能优化的核心价值。
三、精准推荐怎样实现千人千面?
不同于“一刀切”的传统推荐,现代选型软件已具备场景化适配能力。米思米生产软件的用户画像系统显示(表1),汽车行业用户更关注重复定位精度(±0.02mm),而食品机械用户则将清洗便利性作为首要指标。基于20万条行业数据训练的推荐模型,可使选型匹配度提升53%。
典型案例来自某电梯导轨生产企业。其生产线需要同时满足20kg负载搬运与0.1mm级定位精度,SMC选型软件通过“刚需参数优先匹配+柔性参数动态调整”策略,推荐了带伺服控制的双杆气缸方案,并优化气路设计使耗气量减少27%。这种精准度背后,是软件对283个影响因子的权重分析。
未来已来:你的选型工具该升级了
面对日益复杂的工业需求,选型软件已从辅助工具进化为决策中枢。建议企业分三步走:首先通过SMC、亚德客等厂商的免费试用版验证基础功能;其次建立包含工况参数、故障记录等数据的知识库;最终与软件供应商合作开发定制化算法。某注塑机厂商采用该策略后,新品研发周期缩短42%,气缸相关故障率下降68%。
需要警惕的是,软件输出结果仍需人工校验。如某半导体设备商曾因未发现软件默认压力值(0.5MPa)与实际气源(0.4MPa)的偏差,导致气缸推力不足。
智能高效气缸选型软件精准推荐与智能优化全解析的真正价值,在于人机协同创造的“1+1>2”效应——既突破人类算力极限,又保留工程师的工艺智慧。