一、传统制造工艺的“质量魔咒”如何被打破?
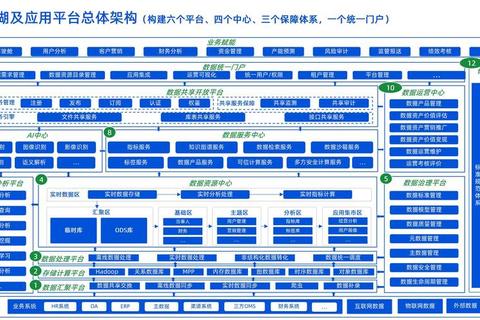
在精密制造领域,一个长期困扰行业的难题是:如何在保证效率的前提下,将复杂零件的良品率从80%提升到99%以上?过去,工程师们依赖经验反复试模,一套汽车压铸模具的调试周期甚至长达3个月,成本超百万。这种“试错式制造”不仅耗费资源,更让企业在新品迭代中步履维艰。而智能高效模流分析软件深度赋能精密制造工艺革新,正在用数字技术重构制造逻辑。
二、智能模流分析能否破解大型压铸件的质量难题?
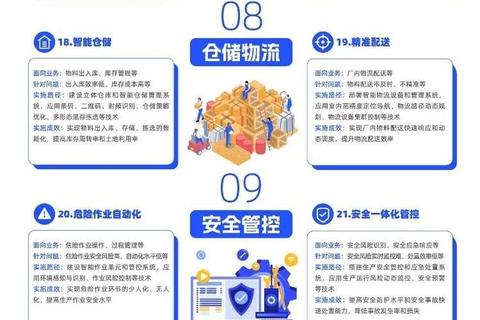
当新能源汽车厂商将后地板、前机舱等部件从数百个零件整合为单一压铸件时,超大型模具的温度场失衡、应力集中等问题成为拦路虎。FLOW-3D CAST软件通过TruVOF®自由液面追踪技术,成功预测宝马汽车16年间开发的200余款压铸件的卷气风险。例如在120寸MINI车型后地板开发中,该软件提前48小时锁定模具热节区域(如图3高亮区),通过优化冷却水路布局,将产品变形量从1.2mm降至0.3mm以内,良品率提升至98.5%。
更值得关注的是其并行计算能力——某电动车企使用256核版本,仅用36小时便完成传统需要7天的模流仿真,开发周期缩短60%。这种高效验证让企业敢于尝试更复杂的结构设计,如特斯拉Cybertruck的一体化底盘,其内部蜂窝状加强筋的流动平衡验证正是依托此类技术实现。
三、多材料精密成型如何实现“零缺陷”突破?
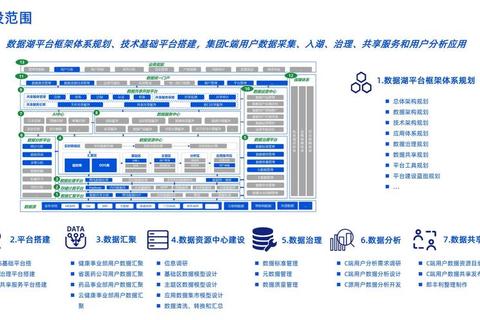
在高端消费电子领域,苹果AirPods Pro耳机的硅胶-塑料双色注塑工艺曾让代工厂陷入困境:0.1毫米的熔接线导致30%产品因透光不均被报废。Moldex3D通过三维热力耦合算法,在虚拟空间中重建了材料交界的分子取向(如图15流动轨迹),最终通过调整浇口偏移0.5mm、模具温差控制在±2℃的方案,使熔接痕强度提升40%。
医疗领域同样受益于此。某胰岛素注射器生产企业采用Moldflow的气穴预测功能(如图9压力云图),在针头与主体连接处增设0.3mm排气槽,将气泡缺陷率从17%降至0.8%。这种微观尺度的工艺优化,让医疗器械的灭菌合格率突破99.99%行业天花板。
四、AI+云计算如何重构模流分析新范式?
传统模流分析面临的最大悖论是:精度越高,计算耗时越长。而智能高效模流分析软件深度赋能精密制造工艺革新,通过三大技术破局:
1. 迁移学习算法:将历史案例库中的5000组注塑参数训练成预测模型,新项目分析速度提升70%。如某家电企业开发空调导风板时,AI自动匹配相似度92%的历史方案,迭代次数从15次减至3次。
2. 实时数字孪生:通过工业物联网采集注塑机压力、温度数据,动态修正仿真模型。某汽车灯罩厂商应用该技术后,将工艺参数自调整响应时间从30分钟压缩到8秒,每年减少废品120吨。
3. 云原生架构:国内某云模流平台支持千核并行计算,单次大型压铸件分析成本从2万元降至800元,中小企业使用率同比提升300%。
五、精密制造的下一站路标在哪里?
对于制造企业而言,把握三个关键决策点至关重要:
技术选型:汽车压铸优先选择FLOW-3D CAST等支持超算的软件,消费电子领域侧重Moldex3D的真实三维仿真能力,中小企业可尝试智铸超云等云端轻量化工具。
人才储备:建议工程师掌握“模流分析+工艺调试”的复合技能,如通过Moldflow锁定气纹位置后,结合模具表面氮化处理(HV≥1000)等物理手段综合施策。
数据资产化:建立企业级工艺数据库,某TOP3手机代工厂通过积累10万组模流数据,使新产品开发周期稳定控制在22天内。
智能高效模流分析软件深度赋能精密制造工艺革新,已不仅仅是工具升级,而是制造思维从“经验驱动”向“数据驱动”的范式革命。当数字孪生体与物理世界实时共振,那些曾经制约精密制造的“不可能三角”——质量、效率、成本,正在被重新定义。